- Home
- Products
-
-
Solids Control Equipment
- Linear Motion Shale Shaker
- Decanter Centrifuge
- Mud Cleaner
- Vacuum Degasser
- Centrifugal Pump
- Shear Pump
- Submersible Slurry Pump
- Mud Agitator
- Mud Gun
- Jet Mud Mixer
- Desilter
- Water Tank
- Mud Tank
- LS1850 Shale Shaker
- Diesel Tank
- MD210 Drilling Mud Cleaner
- Balanced Elliptical Motion Shale Shaker
- Oilfield Drilling Mud Desander
-
Solids Control System
- Drilling Mud Cooling System
- Solids Control System
- Mobile Solids Control System
- Arctic Solids Control System
-
TBM
- Tunnel Boring Mud System
-
HDD
- HDD Mud Recovery System
-
-
- News
- Services
- Marketing
- About Us
- Contact Us
- Videos
Home > KOSUN News >
KOSUN Vertical Cuttings Dryer used in Water-based Mud Field
Mar 30, 2018
Vertical Cuttings Dryer provides operators a important advantage in meeting more and more tight environmental rules for cuttings disposal. The flow of cuttings into the VERTI-G appliance is PLC-controlled and unceasingly fed to yield optimum liquid/ solid separation. Once cuttings area unit introduced into the dryer’s charge hopper, wide spaced, severally adjustable flights unceasingly direct cuttings to the shaker screen surface.
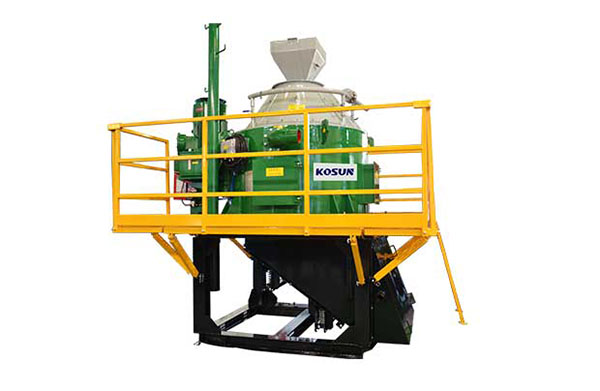
KOSUN G2 vertical cuttings dryer VC2000 serve successfully in water-based mud field and it is the first cuttings dryer successfully applied in water-based mud treatment so far in the world. VERTI-G Cuttings Dryers is very efficient and long lasting as these products are manufactured using high-grade stainless steel obtained from the top vendors. To meet the requirements of our valued clients, we are able to offer these products in various specifications.
The Vertical Cuttings Dryer makes its contribution with its innovative process after the shale shaker completes its task. Cuttings that pass over the shaker typically have an average of 30% to 50% ROC (Retention on Cuttings) when they enter the proprietary auger system and begin to cycle through the VERTI-G cuttings dryer. The initial processing is done with a vertical cutting dryer that utilizes centrifugal force to take advantage of their differing densities to separate the largest portion of the remaining drilling fluid from the cuttings. The processed cuttings are discharged from the vortex dryer into the adjacent shale bin, and then have an average ROC between 4% and 7% once processing is complete. This ROC percentage represents cuttings suitable for immediate disposal requiring minimal if any further stabilization. Processed waste material is lighter, less toxic and is a more cost-efficiency.